Handmade Bokken, Jo, Tanto, ...
At the workshop Aramaki Bokuto Mokojo
Enjoying the quiet summer months, we travelled across Japan to visit the officially recognized workshops manufacturing wooden weapons in Japan "Aramaki Budogu Mokojo", "Nidome Bokuto Seisakujo", "Horinouchi Noboru Seisakujo" and "Matsuzashi Bokuto Seisakujo". These last four companies fabricating wooden weapons are all located in "Miyakonojo", a small town on the peninsula of Kyushu (southern Japan), enclosed by two mountain ranges. In this article we will show all the steps of the making of a Bokken, guided through by an artisan of the workshop Aramaki Bokuto Mokojo, led by master Aramaki, the 3rd.

It is a one hour flight to the city of Miyazaki, then a one hour train ride through the green mountainous forests of southern Kyushu to finally arrive in Miyakonojo, the Mecca of wood crafts we have heard so much of. Based on a flyer, from which the pictures below manufacturing process are taken, we received an explanation we want to summarize in this article.
The history of the Aramaki workshop
The founder, master Aramaki, began woodworking by manufacturing Bokken almost a 100 years ago, in 1921, and a few years later he created this atelier, "Aramaki Budogu Mokojo" (workshop of the fabrication of wooden martial arts equipment) which is now the largest of the four Japanese workshops still in operation. About 15 craftsmen share the manufacturing steps for a production of approximately 250 pieces per day.
This workshop does not offer individual retail but still deals directly with key governmental agencies such as the army, the defense agency and also the police, all three of them being very important customers in terms of the ordered volume.
Among the last four workshops, "Aramaki Budogu Mokojo" is undoubtedly the one offering the biggest choice of different types of wooden weapons, nearly a 100 just for Bokken. Jigen Ryu, Itto Ryu, Jiki Shinkage Ryu... It is almost as if every Koryu (ancient sword school) has its one model. And whenever a Koryu splits into several schools, each school then slightly changes the characteristics of their Bokken in order to make it "unique".
Result: A very impressive amount of different models now exist, without mentioning Jo, Shoto, Tanto, Mokuju (wooden bayonet), Yari (spear), Naginata, Yumi (bow), Nunchaku, Tonfa, etc...


Manufacturing process of a Bokken
First of all, the wood has to be obtained. With the exception of some exotic woods like ebony from Africa, thetimber is harvested locally (see part 2 of the article) by a specialist. The wood is bought in trunks, (impossible to judge if its real quality from the outside,) then sliced by the "Seizaisho", sorted and finally stored for drying.

1. (left): The wood cut into planks and dries in the sun for about one year. Although there are machines to reduce the drying time (down to two weeks!) the drying process is done naturally, because artificially dried wood is more fragile. However, certain workshops use machines at the end of the natural drying process: The Kyushu region for example is very humid and the wood does not always get as dry as necessary.
2. (right): Next, rectangles are drawn on the planks, marking the approximate shape of the Bokken.

3. (left): The outlines are roughly cut by machine.
4. (right): The thickness is then adjusted so that all the rectangles have the same dimensions.

5. (left): The form of the Bokken gets cut, and a machine is used to shape the "Ha" (blade).
6. (right): Further, the Tsuka (handle) is worked on on another machine. At this point we can already distinguish the shape of our future Bokken.
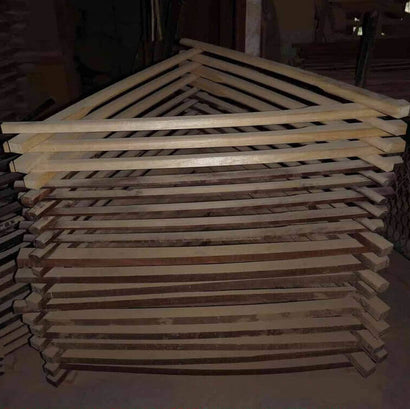

The "pre-cut" Bokken are then stored as shown on the left picture above to continue the drying process in optimal conditions for about one month until the start of the final step: defining the size (picture on the right). The "high-piled" storage prevents uneven drying which would bend the Bokken (the temperature being lower on the ground than on the ground). Note: It is particularly important to store wooden weapons horizontally. (Please check this before you buy them at a shop..).

7. (left): It is at this stage that the work of the craftsman actually begins. Over twenty planes of different angles and curvatures are used. The Bokken is fixed on both ends to allow planing in all directions.
8. (right): Lastly, the finish is done with sandpaper.

9. Varnishing of the Bokken: If needed (optional step).
Of course other steps are necessary for Bokken with a wooden Tsuba (guard) and / or a Hi (groove).


On the left: Ribbon medal, awarded by the emperor "to those who by their diligence in their business have become role models for the people " (usually for farmers and craftsmen). On the right: The personal collection of the Aramaki workshop, wooden weapons manly of Sunuke and Kokutan (ebony).
The pictures 1-9 are taken from a documentation provided by the association "Miyakonojo Bokuto Seizogyo Kyodo Kumiai" and remain the property of the association.
Interview with Aramaki Yasuo Published in 2017
In depth video interview, published 3 years later.
5 comments - Handmade Bokken, Jo & Tanto at the Aramaki Workshop
can i get the bokken signed by the crafter?
yes i know i pay for engraving with laser
great video and interview – a “true artist” at work!
Thank you for this informative article… it’s great to see the history and people who craft.
Hello, I’d like to know if I can buy some of them and how?
I Live in Santiago, Chile.
Thank you
In reply to Luis leyton.
You’ll find all our products here on our website.
Here for weapon sets: https://www.seidoshop.com/collections/aikido-set